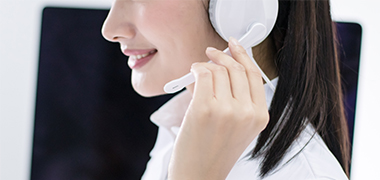
- Contact:Minister Xu
- Mobile:13841408476
- Tel:024-44837288
- Fax:024-44837004
- E-mail:xuming58@126.com
- Web:m.yyyinhang.com
- Address:No.110 XiangHuai Road
Benxi Economic Development Zone
Liaoning Province
Timken Helping to Make Wind Energy More Efficient and Affordable
03 Feb,2020
Timken first ventured into wind energy around 2001, when the industry was in its nascent stages. We were collaborating with a turbine manufacturer to develop a large mainshaft bearing. That experience set us on a course to enter a new market that has grown to nearly 5 percent of our total revenues today, with shipments of more than $1 billion over the past decade. Now, we supply components to nearly every wind turbine manufacturer in the world.
When it comes to the equipment inside wind turbines, the name of the game is performance and reliability. Turbines are often in remote locations like mountain tops and offshore outposts. They must be built to withstand very harsh and dynamic operating conditions. They’re relentlessly pounded with weather extremes–oppressive heat, freezing cold, hail, rain, snow and the very wind they are designed to harness. It’s up to Timken engineers to work with manufacturers to design specialized bearings that are durable enough to take on years of relentless torque and constant environmental challenges.
We made a name for ourselves in the industry by designing mainshaft bearings that enable the enormous blades’ rotation while taking the blunt of applied loads. As you might imagine, these bearings are huge. In the early days, when wind bearings were less than 1 meter in diameter, Timken started developing the next generation of wind bearings that were up to 2.3 meters in diameter—around 7.5 feet. And today, we’re making mainshaft bearings up to 3.4 meters in diameter—over 11 feet!
While many of our competitors focus on a spherical roller mainshaft bearing design, we’ve partnered with our customers to develop innovative tapered roller bearing solutions that increase both durability and reliability. One example is our Timken Tapered Double Inner (TDI) roller bearing. We engineered this design to extend the lifecycles of the largest turbines in the world. We think it’s the optimal bearing to take on the thrust, radial and over-turning moment loads that these large, powerful turbines produce. They’re also power dense, meaning they provide the best performance in the most compact design possible while also reducing operating costs over the life of the bearing.
We offer a whole range of bearing solutions for wind turbine and gearbox manufacturers to meet their precise specifications. And we work with customers to retrofit designs to improve performance and durability of models that were built before we even entered the industry.
While mainshaft bearings got us in the door to wind energy, our acquisitions and innovations over the past decade have helped us present a more complete offering to our customers. We’re also designing gearbox bearings, torque-control devices, couplings, wear-resistant coatings and lubrication systems to help increase the lifecycle, sustainability and efficiency of these machines. And we’re on call to provide maintenance and aftermarket support for turbines all around the world.
While Timken was not involved in wind energy from its inception, what we’ve done over the past two decades has helped advance the industry exponentially. Our close collaboration with turbine manufacturers–coupled with our engineering knowhow–has resulted in more efficient, cost-effective designs.
Today, wind energy has become more reliable and more affordable than ever. Still, it’s a young industry with tremendous upside. In fact, The American Wind Energy Association (AWEA) reports that wind power has more than tripled over the last decade, generating 6.5 percent of U.S. electricity in 2018. At Timken, we’re 100 percent proud of our role in helping to make that happen.