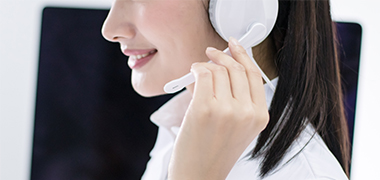
- Contact:Minister Xu
- Mobile:13841408476
- Tel:024-44837288
- Fax:024-44837004
- E-mail:xuming58@126.com
- Web:m.yyyinhang.com
- Address:No.110 XiangHuai Road
Benxi Economic Development Zone
Liaoning Province
Schaeffler is continuously expanding its range of service solutions
13 Feb,2020
Vibration-based condition monitoring systems (CMS) are a proven and highly effective means of avoiding unplanned machine shutdowns and the associated production losses.
Three condition monitoring systems for different customer requirements and plant sizes
Schaeffler OPTIME: New addition brings CMS to the multitude of assets typically monitored only periodically or not at all
Leveraging Schaeffler’s rolling bearing expertise for maintenance personnel and plant operators
Vibration-based condition monitoring systems (CMS) are a proven and highly effective means of avoiding unplanned machine shutdowns and the associated production losses. At the HANNOVER MESSE 2020, Schaeffler will be showcasing OPTIME, a new vibration-based CMS for low-cost applications. OPTIME is a new addition to the Schaeffler CMS portfolio that makes condition monitoring automated and cost-effective for the multitude of indirectly process-critical machines and assemblies typically found in today’s production facilities. The other CMS solutions in the portfolio are SmartCheck, a single-channel system that has been on the market for several years, and the more recently introduced multi-channel system ProLink. A key benefit of all three systems is that maintenance personnel do not need any expertise in vibration-based condition monitoring in order to install them. The same simplicity also applies to analyzing the output data, since the analysis is done by Schaeffler algorithms. These three systems mean Schaeffler can provide vibration-based condition monitoring solutions for any requirement scenario.
OPTIME: For the condition monitoring of entire facilities
OPTIME comprises multiple wireless, battery-powered vibration sensors that transmit KPI data and raw vibration and temperature data for all machines in the production facility to the Schaeffler IoT Hub via a dedicated mesh network. The data are automatically analyzed by special Schaeffler algorithms, and the results are sent to the associated app, where they are displayed in a clear and readily transparent manner in a range of user group-specific views. The system is readily scalable because installing and integrating a new measuring point takes only a few minutes. OPTIME offers cost savings of some 50 percent compared with offline measurements and significantly outperforms other wireless CMS systems in terms of quality. With OPTIME, in-house maintenance crews and external service contractors receive several weeks’ advance warning of impending problems as well as specific recommendations on remedial measures, so they can easily plan their maintenance work, manpower requirements, and spare parts procurement in a timely and cost-efficient manner.
SmartCheck: For stand-alone, process-critical machines
Designed for permanent machine and process monitoring, the Schaeffler SmartCheck is a wired, online monitoring system, complete with integrated web server and learning mode. Its ability to handle variable rotation speeds and process information and, more especially, its differentiated signal recording make it ideal for monitoring process-critical machines in small-scale plants. KPIs and alarm states can be visualized using any standard browser or transmitted directly to the control system via Ethernet using the module’s integrated communication protocol. For customers wishing to use Schaeffler’s online digital services, the SmartCheck module can send its data via OPC UA interface to the Schaeffler IoT Hub.
ProLink: For process-critical larger-scale machines and facilities
ProLink is the SmartCheck module’s “big brother” for process-critical machines with between four and 16 measuring points. It is a wired, modular multi-channel condition monitoring system that can record and analyze data on vibrations and several other variables. As with the SmartCheck module, the ProLink’s firmware features both Schaeffler-defined parameters and a learning mode for machine-specific adaptation. The ProLink module can be mounted in a switch cabinet and is integrated into the customer’s infrastructure via a Fieldbus module. The system supports OPC UA, and other protocols such as Profinet and CC-Link IE are in the pipeline.
ConditionAnalyzer: Digital service for automated analyses
Schaeffler’s ConditionAnalyzer is a digital service for all Schaeffler systems and other commonly available condition monitoring systems. All vibration-based condition monitoring systems can capture and visualize vibration data, but figuring out what those data mean in terms of damage progress and severity and, more especially, bearing condition requires in-depth domain knowledge of the various components involved. The Schaeffler ConditionAnalyzer software provides this level of condition information automatically, enabling users to quickly determine whether the bearing in question needs to be replaced and when, thereby largely avoiding unplanned shutdowns. With ConditionAnalyzer, maintenance crews no longer have to spend precious time manually analyzing and interpreting all of the vibration data generated by their CMS systems. ConditionAnalyzer can easily be integrated into remote maintenance systems and existing IoT platforms via a REST API.