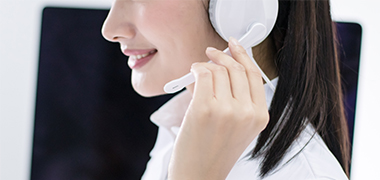
- Contact:Minister Xu
- Mobile:13841408476
- Tel:024-44837288
- Fax:024-44837004
- E-mail:xuming58@126.com
- Web:m.yyyinhang.com
- Address:No.110 XiangHuai Road
Benxi Economic Development Zone
Liaoning Province
Phase Management as a Strategy to Reduce Gear Whine in Idler Gear Sets
13 Jul,2020
Gear whine is caused by transmission error, shuttling, friction, impacts, lubricant entrainment and air entrapment (Ref.1). While the list of gear noise factors is fairly long, it should be recognized that the typical gear noise problem is not a result of lubricant entrainment or air entrapment. Impacts are due to corner contacts that might occur when the teeth just come into contact or due to interference at the root. Both are usually avoided by good gear design. Corner contact is avoided by applying appropriate relief to the teeth. Interference is avoided either by undercutting the flanks of the pinion teeth, by using long addendum pinion and short addendum gear teeth, or by increasing the pressure angle (Ref.2). That leaves transmission error and other mesh forces.
The mesh forces are usually described as line of action (LOA) and off line of action (OLOA) forces, otherwise known as normal and tangential forces. The greatest line of action forces are from transmission error, which is a line of action displacement, and is the focus of this paper. Shuttling forces of helical gears also act along the line of action. The position of the force vector representing the mesh force shuttles axially as the gears rotate through one tooth mesh sequence. The bearings must react to the axial change in load position and therefore see a change of force that varies at tooth mesh frequency. Tooth friction forces are off line of action forces (Ref.3). Shuttling and friction forces are generally regarded to be of lesser importance to gear noise but become important when the transmission error is very small.
Transmission error is the driven gear’s deviation from perfect conjugate action and is the result of manufacturing geometry errors; gear tooth, shaft and housing deflections; mesh stiffness variation; and dynamics (Refs.4–6). The dynamic forces generated within the gear mesh because of imperfect conjugate action are reacted at the bearings supporting the gears in the housing. These dynamic forces on the housing excite the housing causing it to vibrate. The housing surface vibration couples with the air causing pressure fluctuations that travel as sound pressure waves to our ears; we hear them as sound. Reducing transmission error is the preferred approach to reducing gear whine.
The forces acting in the gear mesh are made up of DC and AC forces. The DC mesh force is the necessary static force required for the gears to transmit power. This force is present by design. Static forces cause certain design challenges such as bearing life and shaft and housing deflection, but they don’t cause gear noise. Gear noise is the result of the AC forces from transmission error, shuttling, and friction, and are unintentional. These dynamic forces are tiny in comparison to the static forces. In the example to be discussed later, the DC mesh forces are in the magnitude of the weight of a pickup truck while the AC forces are less than a bag of dog food (Fig.1). It is only these small AC forces that we are interested in from a noise perspective. Because all the bearing forces are resolved within the gearbox, summing all bearing reaction forces on the housing results in zero, yet there is noise. That is because the forces act on various locations of the gearbox.
Consider the two gear mesh of Figure 2. These transmission error forces at the bearings are in phase, that is, they reach maximum values simultaneously (assuming the gears’ and shafts’ first natural frequency is sufficiently greater than the mesh frequency). Transmission error forces are managed by making gear microgeometry modifications. While transmission error can theoretically be reduced to zero at a single load, it is the gear designer’s challenge to make transmission error small over a range of loads (Refs.7–8). Transmissions that operate over a wide range of speed and load are especially challenging and the designer then must make choices about where in the operating space it is imperative to minimize transmission error.